Aluminum PCB
General introduction of Aluminum PCB
Aluminum PCB is a metal-based copper clad laminate with good heat dissipation function. Generally, a single-sided panel consists of three-layer structure, which are circuit layer (copper foil), dielectric layer and metal substrate. Commonly found in LED lighting products. There are positive and negative sides, the white side is for soldering the LED pins, and the other side is aluminum, which is generally applied with thermal paste and then contacts the thermally conductive part. There are also ceramic substrates and so on.LED aluminum PCB is PCB, which is also the meaning of printed circuit board, but the material of the circuit board is aluminum alloy. In the past, the material of our general circuit board was glass fiber, but because the LED generates heat, the circuit board for LED lamps is generally aluminum PCB can conduct heat quickly, and the circuit boards for other equipment or electrical appliances are still glass fiber boards.
Working principle of aluminum PCB
The
surface of the power device is mounted on the circuit layer. The heat generated
by the device is quickly conducted to the metal substrate through the
dielectric layer, and then the heat is transferred out by the metal substrate,
thereby realizing the heat dissipation of the device (see Figure 2).
Compared
with the traditional FR-4, the aluminum PCB can minimize the thermal
resistance, so that the aluminum PCB has excellent thermal conductivity;
compared with the thick-film ceramic circuit, its mechanical properties are
excellent. In addition, the aluminum PCB has the following unique advantages:
It meets the requirements of RoHs; it is more suitable for the SMT process.
Extremely
effective treatment of thermal diffusion in circuit design schemes, thereby
reducing module operating temperature, extending service life, improving power
density and reliability; reducing assembly of heat sinks and other hardware
(including thermal interface materials), reducing product volume, reduce
hardware and assembly costs; optimize the combination of power circuits and
control circuits; replace fragile ceramic PCB to obtain better mechanical
durability.
Structure composition of aluminum PCB
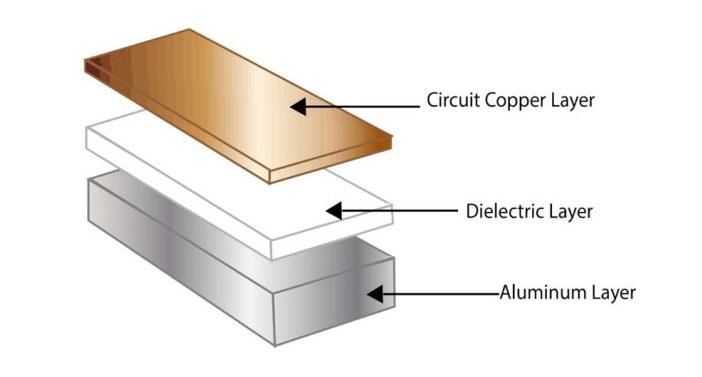
1. Circuit layer
The circuit layer (generally using electrolytic copper foil) is etched to form a printed circuit for assembly and connection of devices. Compared with the traditional FR-4, with the same thickness and the same line width, the aluminum PCB can carry higher current.
2. Dielectric layer
The dielectric layer is the core technology of the aluminum PCB, which plays the functions of bonding, insulation and heat conduction. The aluminum PCB dielectric layer is the largest thermal barrier in the power module structure. The better the thermal conductivity of the dielectric layer, the more conducive to the diffusion of heat generated during the operation of the device, and the more conducive to reducing the operating temperature of the device, thereby achieving the purpose of increasing the power load of the module, reducing the volume, prolonging the life, and improving the power output.
3. Metal substrate
Which metal is used for the insulating metal substrate depends on the comprehensive consideration of the thermal expansion coefficient, thermal conductivity, strength, hardness, weight, surface state and cost of the metal substrate.
Choose AllWinPcba for your aluminum PCBs
Thanks
to the premium performance, aluminum PCBs have been widely used in the areas
including LED lighting, automotive, audio device, power conversion, power supply,
communication electronic equipment, motor drivers, etc. AllWinPcba provides
one-to-one service to better suit your needs of aluminum PCB, we welcome your
inquiry about our Aluminum PCBs: svc@allwinpcba.com
Aluminum PCB Instant Quote
PCB Capabilities
PCBA Capabilities
SMD Stencil
Printed Circuit Boards
Product Show
Contact Us!
Our customer serviceready for your PCB
1.608.698.5398
SVC@allwinpcba.com